Running out of manufacturing capacity and considering building a new facility? You’re not alone. Many industrial manufacturing operations in the Chicagoland area have reached the limits of their current footprints after decades of expansions and retrofits. It’s left many to believe that building new is the only option.
Such was the case for ODM Tool & Manufacturing in McCook, Illinois. They’ve provided custom precision metal stamping for top brands in the United States for nearly a century, including those in the automotive industry. To stay on the leading edge, they needed to continually invest in new technologies, including a new metal stamping press.
The problem? Yet another addition wasn’t possible due to limited real estate, and multiple manufacturing facility expansions over the years made it nearly impossible to configure the 1,200-ton piece of equipment into their existing workflow.
Or so they thought.
How Multiple Building Expansions Can Limit Renovations
Over the years, multiple building additions of varying construction methods and ceiling heights can create a hodgepodge of work areas that limit productivity and capacity. Technically, a facility may have ample square footage on paper, but because of the way walls and workspaces are configured, there may not be enough space to introduce new equipment or production lines.
ODM Tool & Manufacturing realized this pain point. Their older production facility had an inefficient layout and low ceiling heights, and employee locker rooms were centralized in an area that impeded production workflows.
Adding to the challenge was the construction technique of ODM’s most recent addition — a pre-engineered metal building with high-bay ceilings to accommodate a crane. Pre-engineered construction is designed with tight tolerances to accommodate specific requirements, making modifications extremely complex.
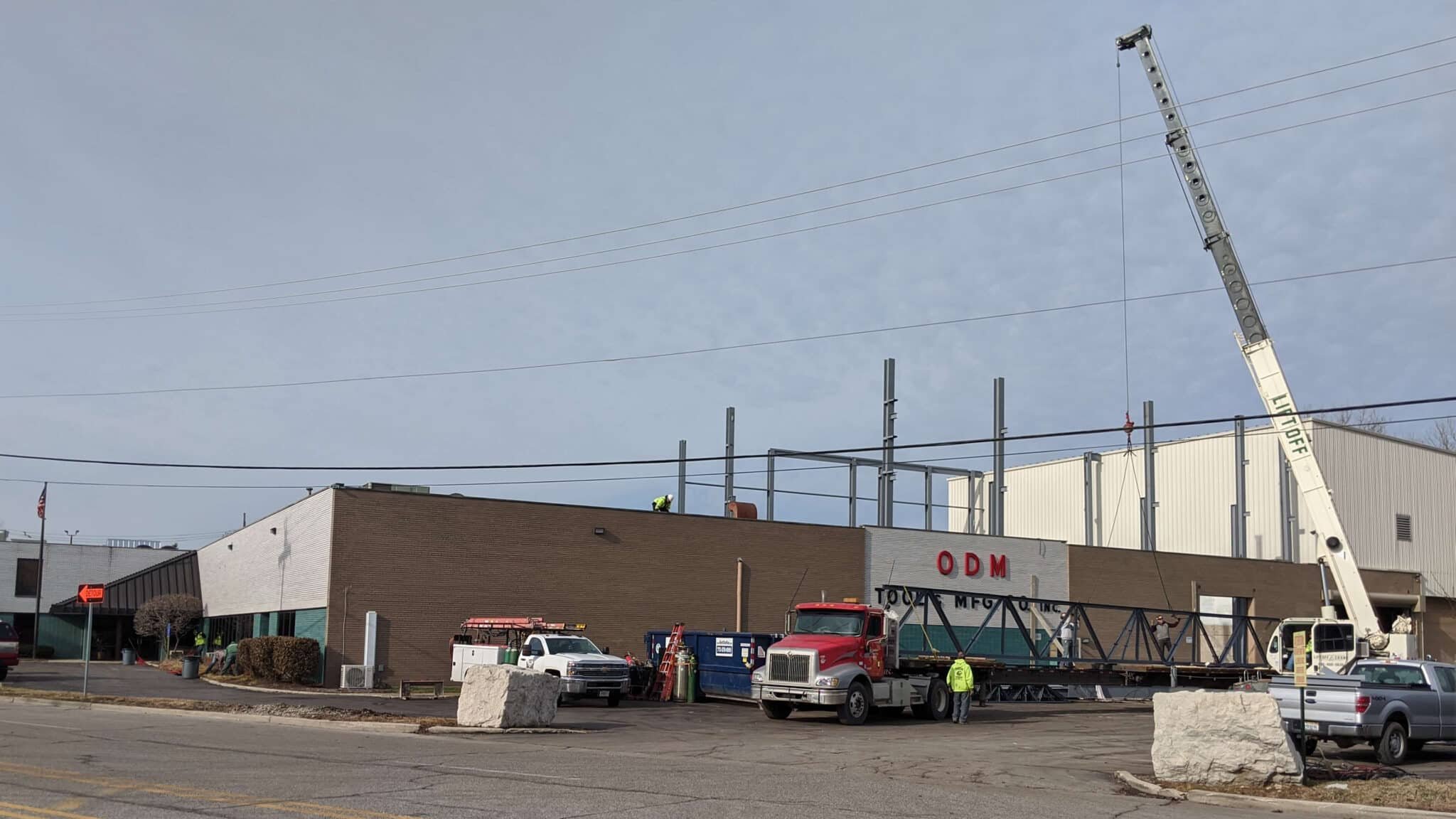
Design-Build Solutions for Complex Manufacturing Facility Renovation
The design-build experts at Raffin Construction in cooperation with the owner’s representative, J.L. McGuire & Associates, designed a plan to join the old and new sections of the facility into one. After handling the acquisition of all permits, Raffin retrofitted the older ODM facility by raising the roof and demolishing and relocating the employee locker rooms to another part of the building. They engineered a solution to reinforce structural components and removed a column and partial walls without compromising the structure’s integrity.
Rather than two disjointed sections of the building, Raffin Construction created an expansive, well-lit open area with high ceilings all the way across. Such a modification allowed for the overhead crane to expand into the older part of the facility to service both presses and move completed projects to the loading dock.
To accommodate the massive metal stamping press equipment, Raffin had to excavate a 15-foot-deep foundation pit and design and build a soldier pile and lagging earth retention system at the perimeter of the pit to keep the excavation and the building stable.
Raffin also needed to assess and plan for water pumping and displacement. Water tables and soil types vary widely in the Chicagoland area, requiring proper analysis, and preparation. They then installed the reinforced concrete foundation with cutouts and inserts built to precise tolerances to accommodate the press specifications and 1,200-ton weight. A large trench with a conveyor system was also built to carry scrap outside the building from the existing press and new equipment.
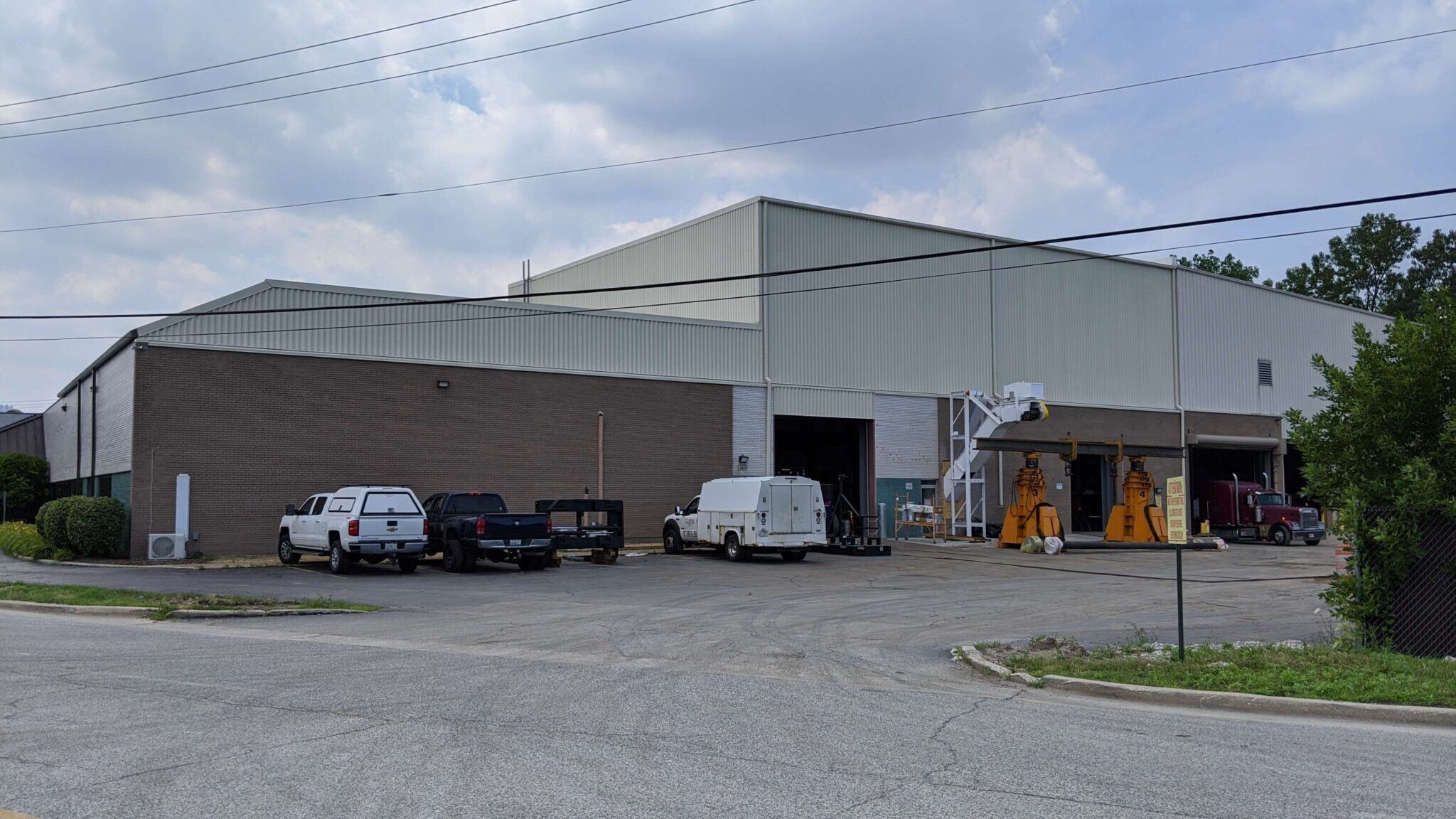
Minimizing Downtime During Renovations
Another challenge of renovating an existing facility is potential downtime for production lines. Prolonged shut-downs to accommodate construction crews and retrofitting requirements are often a non-starter for industrial manufacturers.
For the ODM project, Raffin leveraged a phased construction approach, allowing the company to remain operational. ODM and Raffin worked together closely during the planning phase to schedule construction activities in a way that minimized disruption. As a result, ODM hit all their production deadlines.
More importantly, ODM Tool & Manufacturing was able to add a second press, expand production capacity, and improve workflows with a state-of-the-art facility that will serve its customers for years to come. Furthermore, the new locker rooms that once impeded production lines were rebuilt in another area of the facility, helping employees feel appreciated and cared for.
If your organization is challenged with choosing between a manufacturing facility expansion or renovating an existing facility to meet the needs of an increasingly competitive market, contact the experts at Raffin Construction. We can help determine options and will work closely with you or your representative to deliver a customized solution, from design-build services to construction to custom concrete finishing and foundation work, and everything in between. Contact our team today.